july 15
The Milk Factory prior to works commencing on site. The property comprises of a basement and ground level which extend from Wellington Place to Constitution St. The upper floor fronts Wellington Place. The ground floor and basement had formed a garage and retail space for Pentland Component Parts, with the upper floors operating as office space and a kitchenette. Historically however the property formed a distribution centre for Nestle Milk, being just around the corner from the nearby Leith Central Railway Station which used to be at the foot of Leith walk and is as of 2017, a dental surgery
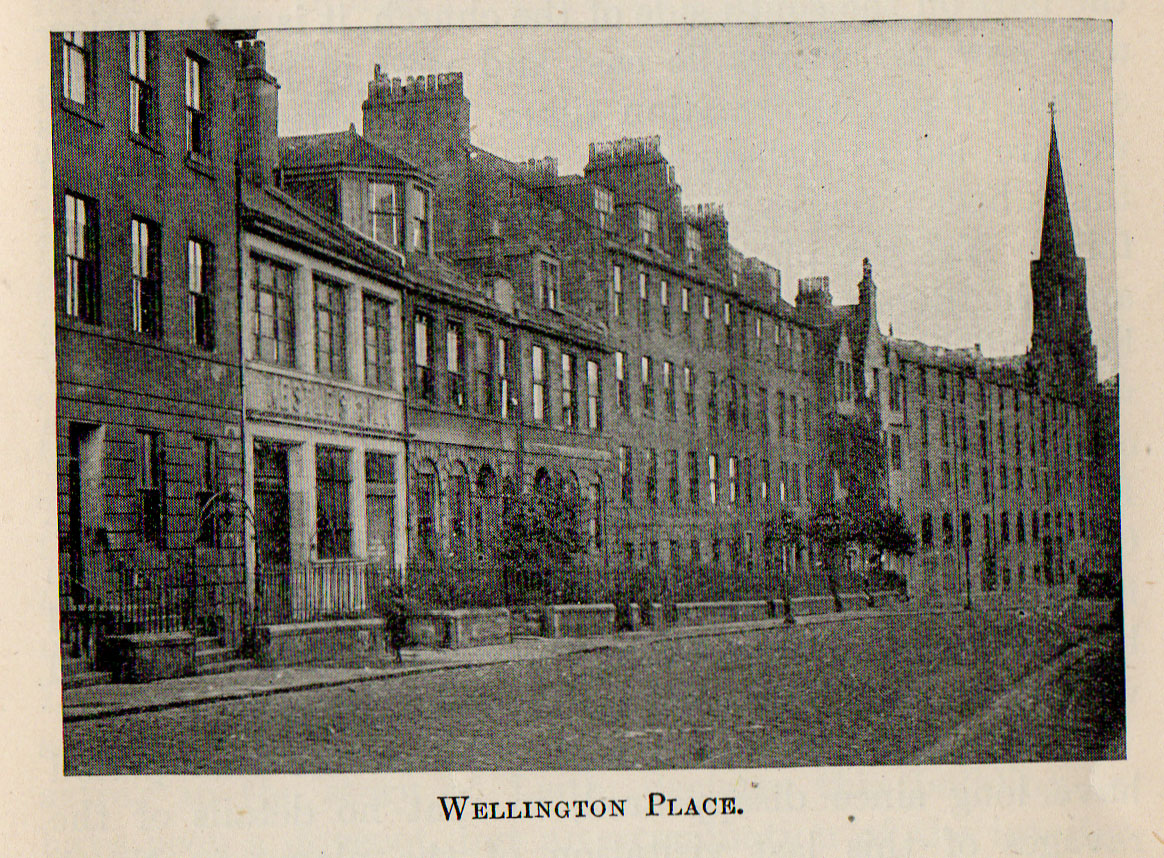
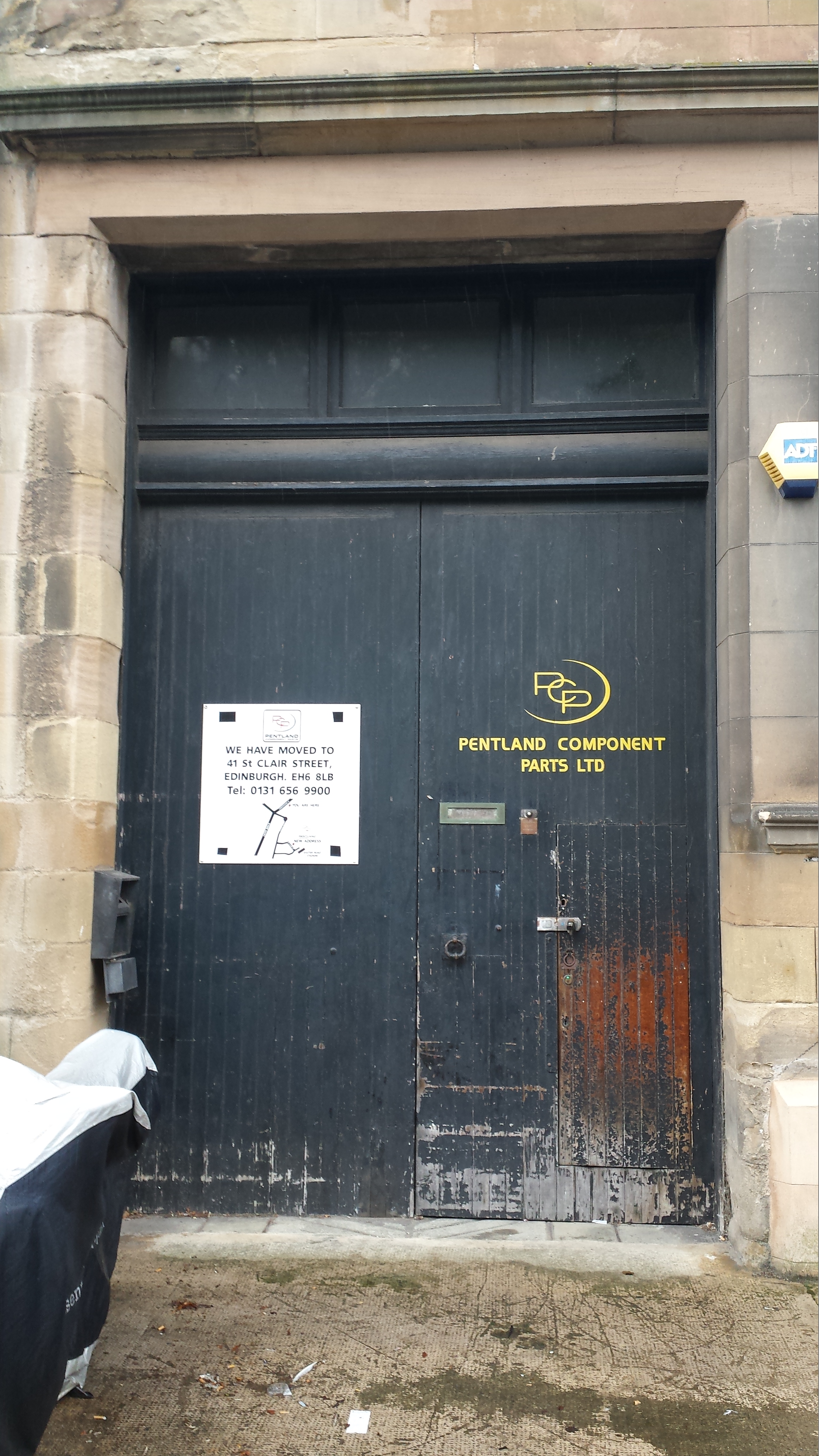
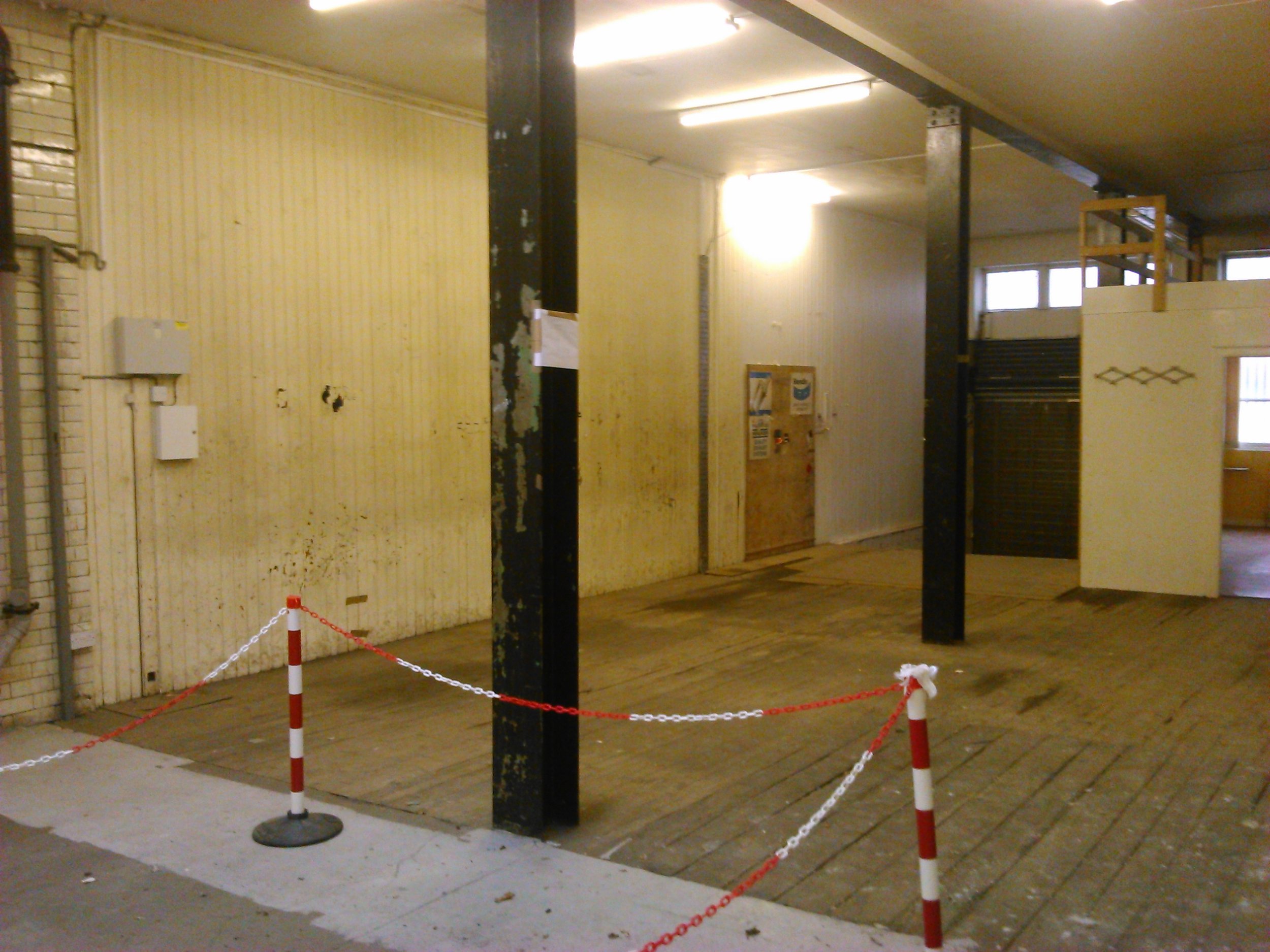
AUGUST 15
Work starts on site stripping out partitions and linings on the first floor. The original tongue and groove was retained for the walls of one of the proposed bedrooms and removed elsewhere to expose red brick in the other rooms and random rubble masonry to the stair. On the ground floor, the proposed layout for the landscaped courtyard is marked out in duct tape to provide a sense of scale for the client.
September 15
Removal of the central roof begins. Much of the original deep red wood timber beams are removed from site to the workshops of SJS to be de-nailed and dressed for use in the construction of the internal furniture. It will be used in the kitchen units as well as for the snug sideboard and bathroom vanity units. Glazed white brick is carefully removed from internal partitions, cleaned and set aside for reuse in the kitchen island. The upper rear wall which can be seen constructed of red brick, will also be removed and rebuilt in timber stud. This allows better control of the thermal efficiency and window openings.
All internal partitions to the first floor are removed and the elevator, which was once concealed behind linings, is now revealed. Faced with this New York loft style space it was difficult to overcome the desire to leave it open-plan. Many opportunities can present themselves along the way, especially when uncovering pleasant surprises during renovations and refurbishments - often it's knowing (or not) which ones you want to take...
october 15
The new rear wall to the ground floor is under construction - this forms the divide between the internal space and the proposed courtyard. There will be a large triple sliding door here to provide easy access and views to the garden. The red brick from the first floor rear wall has been removed, cleaned and set aside for reuse as the snug fireplace. The upper flat roof is replaced with a Bauder felt build-up. This is a hardier surface finish than traditional single-ply membrane and comes with a great guarantee, fitted by B&D Roofing.
Drilling begins for the two boreholes of the ground source heat pump and the head bricklayer builds a small example wall for the apprentice. Exciting stuff! :)
november 15
With the property spanning across the block, the rear entrance to Constitution St required some remodelling. A new steel stair was fitted to give direct access tot he basement to allow large items to be placed in and removed from storage without having to enter the house proper. The stair was designed and fabricated by Loanhead Engineering .
As part of the refurbishment works we had allotted a provisional sum towards reparations to the roof as some leaking had been suspected. Following further surveying it was recommended that the slates be replaced.
Internally, some linings are fixed and the first fix of the electrics begins to take place.
december 15
We were keen to pour the concrete floor prior to Winter setting in to provide time for it to cure over the festive season. Fraser Bruce provided a fantastic poured concrete floor with an industrial finish - one which required only the least amount of polishing and grinding. It was an interesting choice by the client as highly polished concrete floors are generally favoured however this restraint on a high finish resulted in a floor that was highly suited to it's industrial past.
You can see the network of plastic piping that forms the underfloor heating. With such a large area and thermal mass of concrete, underfloor heating allows the floor to become one radiant surface, reducing the need for wall hung radiators and providing an efficient and comfortable control of the internal temperature. The extent of services in the building can be seen - some of which is so satisfying it seems a shame to cover it up!
The 'slot light' to the first floor is well defined now and provides a large amount of natural light to the otherwise dark hall space.
January 16
Internal linings are practically complete and the plaster skim coat has begun. General wall construction may compose of plasterboard butted, taped, filled and sanded to relieve the joint lines, following which it is generally given a 'mist' coat (watered down paint) prior to final decoration. Here, we opted for a complete skim of plaster to offer a seamless, smooth finish. Plasterwork is certainly an artisan skill and something of a work-out...
The double height connecting void to the dining area and first floor has been neatly formed and again provides a good quality of natural light to enter into the deep plan - a discussion has begun on whether or not the flue to the wood burning stove should pass in front, or to the side of it.
The new steel stair to the front entrance is fitted and ready for painting.
February 16
The windows arrive on site! The property has suffered from not being water-tight for the winter. This was due in part to issues at the production plant in Norway delaying delivery and then the gut wrenching destruction of the windows in transit across the North Sea. We decided to order windows from Blair's in Glasgow, who as it turned out, had a much shorter lead time. The drama didn't stop there though as once the windows arrived on site we noticed they had white weather bars - an unwelcome distinction from their proposed dark grey.
Finishes become more prominent as the timber floor is stripped, ready for staining with Osmo oil. The existing timber doors are also back from being chemically stripped and dipped. The process is quite aggressive and some doors can't stand up to it but the quality of the original doors is very good indeed and the result is stunning.
We finally get to see the kitchen island being formed in the beautiful glazed brick - note the lovely curved bricks forming the corners
March 16
The most exciting element is final in place - the larder scissor door! Reclaimed from the existing elevator (sadly removed in totality) the cast iron scissor door was fitted in place, replete with original recessed floor track and latch mechanism.
Second fix electrics are almost complete and we finally get to see the clients own unique style populate the space. A fantastic Lutron system was specified and fitted by Scott of LightMedium. The system can be programmed to control many lights at the push of a button to pre-selected 'moods'. Whether you're winding down for the evening, throwing a dinner party or getting up first thing at the weekend, one push of a button creates the perfect lighting.
Another exciting element is the furniture beginning to turn up on site and seeing the reclaimed wood being given a new lease of life. Old timbers have been thinned down and stained, ready for lining the dining room wall.
The red brick has finally been reused to form the fire place in the snug. Timber form work creates the mold for the concrete work top.
April 16
The works are approaching practical completion at this stage. Kitchen units have arrived on site and are being fitted. Much of the internal finishes are in place. Siberian larch louvres are fitted to the courtyard to provide privacy from adjacent buildings and stained Scots Larch cladding from Russwood provides a natural finish to the courtyard. The green roof has been installed on the new flat roof to the living area and is already beginning to attract birds and insects.